ESG strategy and management
Rusagro is a Russian systemic company that provides the domestic households with such food products as sugar, pork, vegetable oil, margarine and mayonnaise, and industrial fats. The sustainability of the Company's business is necessary to maintain national food security and the national independence from food imports.
CONTRIBUTION TO UN SDGs
Mission, vision, values and strategy
GRI 102-16 GRI 102-26In keeping with the mission To Make People's Lives Longer and Better, the Company focuses on long-term growth and responsible conduct of business, accommodating the interests of all stakeholders. In 2008, Rusagro went ahead with its "field to shelf" concept, which implies a vertically integrated business model in food production. As of 2021, the Company continues to follow out this concept.
In 2021, Rusagro began developing a formalised ESG strategy, which is expected to be approved in 2022. The idea behind the new strategy is to support the Company's stable and sustainable growth, improve the transparency of non-financial information about its operations, and create added value for stakeholders.
Rusagro's Board of Directors plays a key role in setting strategic sustainability priorities for the Company's management. Among other things, the Board determines the fundamental values that guide Rusagro's business and oversees the progress on the corporate strategy.
The Company's mission is based on three basic principles: minimising its negative environmental impact, creating positive externalities for society and maintaining high standards of good corporate governance. The ability to align Rusagro’s practices with global sustainability and responsible business conduct trends is now a prerequisite for achieving strong economic performance and ensuring the long-term growth of the Company.
Rusagro traditionally prioritises following areas:
- Business expansion;
- Increasing the sales of retail products and brands;
- Digital transformation and innovations;
- Development of human capital.
Rusagro aligns its sustainability strategy with the UN Sustainable Development Goals (SDGs).
Rusagro is guided by the following corporate values:
Development stages of Rusagro's ESG management system
- Appointing a person in charge of formulation and implementation of the ESG agenda
- Laying out an action plan to navigate the ESG agenda
- Analysing of the maturity of ESG practices in the Company
- Release of the first ESG report under international GRI standards
- Approval of the first ESG strategy
- Appointment of ESG Curator on the Board of Directors
- Obtaining S&P CSA and CDP ratings (Carbon Disclosure Project)
Rusagro’s strategic approach
Goals:
- to minimise the negative environmental impact
Measures:
- employing sustainable agriculture methods
- safeguarding the soil health
- mitigating emissions of greenhouse gases and pollutants
- reducing energy consumption and improves energy efficiency
- reducing load on water resources by optimising water consumption
- minimising pollution by effluents
- reducing the amount of waste produced
Goals:
- to enhance the attractiveness of its employer brand and the social development of the regions where it operates
Measures:
- providing training for employees and facilitates their career growth
- creating safe working environment
- ensuring equal rights and opportunities
- offering social support and financial motivation
- increasing employee engagement
- investing resources in supporting and developing local communities
Goals:
- to ensure high quality and sustainability of corporate governance
Measures
- providing a transparent ownership and management structure of the Company
- disclosing non-financial information in a timely manner
- actively engaging with investors and shareholders
- enforcing business ethics and applicable laws
- building responsible supply chains
- To achieve high economic performance
- To ensure the long-term sustainable growth of the Company
- To serve the interests of stakeholders
Contribution to the UN SDGs
UN SDGs | Rusagro's contribution |
---|---|
Rusagro is committed to creating new jobs in the regions where it operates and offers fair and decent remuneration for its employees In 2021, the Company employed a total of 17 ths full-time employees and 3,000 temporary employees Rusagro does not use forced or child labour and upholds international human rights and labour standards | |
As a producer of key mass-consumption agricultural products, Rusagro aims to provide consumers with quality food at reasonable prices and is therefore aware of its role in ensuring national food security | |
Rusagro cares as much about the health of its employees as it does about the health of its consumers. The Company has a comprehensive employee health programme and maintains high product safety standards | |
Rusagro's programme to support local communities and social development in the regions where it operates covers charitable projects that address the development of educational infrastructure and various educational events, amounting of total of RUB 38.8 mn allocated to promote education in the regions of presence in 2021 Moreover, Rusagro is strongly focused on the development of its own employees. Over 19 ths employees received training in 2021, both in face-to-face and distance formats | |
The Company has a zero-tolerance policy towards all kinds of discrimination, seeing diversity as a source of inspiration and opportunity At the end of 2021, the overall proportion of women in the Company was 35%, while among white-collars this figure reached 60% | |
All of the Company's business segments are exploring opportunities to incorporate the circular economy principles, reduce the amount of waste produced and re-use resources For example, lime defecate, a by-product of sugar plants, is apllied as a fertiliser in the Company's fields | |
Although the regions where Rusagro operates are free of any risks associated with the scarcity of water resources, the Company apples itself to optimise water consumption and minimise pollution with effluents The Company implements water recirculation and reuse systems and automates water consumption control systems The year-on-year results showed the decrease of 4,000 cubic metres in the total water consumption. Concurrently, the Company is working towards improving the quality of effluents | |
Air cleaning equipment and dust & gas catchers are mandatory pre-requisites for the reduction of atmospheric emissions Another focus area of the Company's measures covers the energy consumption reduction and energy efficiency improvement Reducing energy consumption enabled the companies of the Oil and Fats Segment to make total savings of more than RUB 50 mn in 2021 | |
In 2021, Rusagro established a specialised company, Rusagro Technologies, for centralised management of process-related innovations Innovative projects run by the Company during the reporting period include the optimisation of machinery route in the field, the design of a freight transport planning algorithm, the development of an intelligent management system for raw material procurement and delivery, the integration of business planning for sales, logistics optimisation, the promotion of video analytics as a management data collection tool and the development of tool-based monitoring of equipment condition | |
In using fertilizers, Rusagro obeys regulations that envisages environmental safety measures to eliminate the risk of soil pollution The Company also invests in land reclamation |
Sustainable development approach
GRI 103-2As far as Rusagro's sustainability management is concerned, there are six focus areas.
Fighting the global climate change
Over the last century,
All the above led to an increase in global average temperature, which in turn had a negative impact on the global climate. Such warming brings with it the risk of melting glaciers, rising global sea levels and increasing the frequency of extreme weather events such as droughts, forest fires and floods. Changes in temperature, ozone depletion, lack of water and nutrients could adversely affect crop yields and therefore jeopardise the food security of the Company's sales regions and its economic performance.
Being a responsible company, Rusagro takes into account that the agricultural business is a significant source of anthropogenic greenhouse gas
Circular economy
Limited natural resources and the growing amount of waste generated pose a serious risk to the long-term sustainability of the economy. Annual human consumption of resources already far exceeds the planet's ability to reproduce them, while waste is destroying the environment, causing severe damage to soil health, water resources and fragile ecosystems. The agricultural sector in particular be heavily reliant on resources such as water, fertile land, phosphorus and fossil fuels. Reducing excessive consumption of water, fossil fuels and phosphate fertilisers will not only help reduce the negative environmental impact, but will also ensure the sustainability of business in the future.
The Company's emphasis in this area is on optimising water consumption, reducing the amount of waste produced and seeking opportunities to embed the principles of a circular economy in its operations.
Sustainable agriculture
To meet the food needs of present generations in a way that does not deprive future generations of the same opportunity, agribusinesses now need to take steps to integrate the principles of sustainable agriculture, and this is the issue Rusagro is adressing now. This approach will help reduce the negative impact on soil health and thereby prevent premature soil depletion. Moreover, a more caring attitude towards fragile ecosystems will be beneficial for the overall level of environmental well-being in the regions where the Company operates and will improve the lives of local communities.
Rusagro's agricultural activities are based on an adaptive-landscape farming system, which involves ensuring agro-landscape sustainability and restoring soil fertility. When planning the optimum quantity of products, the Company takes into account environmental factors, available natural and production resources and market needs.
Caring for employees and supporting local communities
Rusagro's employees are one of its most valuable assets. Attracting and retaining skilled staff in the agricultural sector is a certain challenge for business today. In order to remain an attractive and prestigious place to work and meet the changing interests, priorities and demands of potential employees, agri-business calls for corresponding changes. To fit the times, Rusagro concentrates on developing internal human capital in order to improve the attractiveness of its own brand for agricultural experts. The Company builds an innovative and inclusive environment that is conducive to the development of career and professional potential.
Being consistent with its mission to improve people's quality of life, Rusago orchestrates its activities in a way that maximises positive externalities in the regions where it operates through the investment of resources and comprehensive all-round support for the social development of local communities. The Company's charitable projects and social investments cover the promotion of education and hosting of cultural and sporting events.
Product quality
Consumers of our products are one of our most important stakeholders, and it is therefore crucial to ensure the safety of the food produced and supplied by Rusagro. Maintaining high standards of product quality control is a pre-requisite of a high level of customer satisfaction.
All of the Company's business units have quality control services responsible for the safety of their products, and all production sites are also certified for compliance with international quality management and food safety standards.
Animal welfare
Caring for the welfare of animals in the Meat Business means much to Rusagro, and it makes sure that animal housing and management conditions remain humane at all stages of production by employing practices that ensure the so-called 'five freedoms of animals', which include the proper provision of food and water, protection from pain, injury and disease, minimisation of stress and discomfort, and ensuring that animals can lead a natural life.
Business ethics and anti-corruption
High standards of business conduct and ethics, as well as compliance of the Company's operations with all legal regulations within the framework of applicable law, are an important component of modern responsible business. Rusagro's activities are aligned with an internal Code of Business Ethics and Conduct, which is binding for all employees and suppliers. In addition, the Company closely monitors compliance with applicable laws and actively tackles any issues of corruption and fraud.
Responsible supply chains
A responsible approach to business is to be followed not only by the Company, but also from its suppliers to cover a sustainable value chain for Rusagro's products. To minimise the negative environmental and social impacts of Rusagro's products, there is a continuous improvement model for supply chain management, ensuring the transparency of procurement processes, assessing ESG risks, selecting responsible suppliers and automating the procurement system.
ESG riskS management
gri 102-15gri 201-2Timely identification of risks related to sustainable development and elaboration of preventive controls are at the core of the Company's strategy. Each year the Board of Directors reviews a list of the most significant risks identified and reconsiders the strategy accordingly. Thus, Rusagro identified seven types of risks in 2021 (listed in the Company's 2021 Annual Report), which, if realised, could potentially have the greatest impact on the Company's performance.
All but one risks identified relate to the sustainability area; the one risk out is associated with a drop of prices for Rusagro's products due to a number of market factors, which are beyond the Company's control, for example, an increased supply from competitors, lower purchasing power of households, or a global decline in the prices of similar products.
The other six risks are sustainability-related (see the Sustainability Risks table) and can be divided into two main categories: non-climate change risks and climate change risks.
Non-climate change risks
The political risks highlighted by Rusagro include possible changes in national policy on price controls for marketed products, as well as changes in tax and export/import regulations. The imposition of price ceilings, duties and quotas on food exports will limit our ability to maximise revenues, while higher taxes will reduce net profits.
Another group of risks cover human errors in the planning and implementation of process steps, which can negatively affect the Company's performance and increase the cost of production. Agronomic errors can ruin the results of the Agriculture and Sugar business segments, while procedural violations at the meat processing plants can compromise the Meat Business.
The coronavirus pandemic evidentiated the vulnerability of global business to such events. The emergence of new epidemics or pandemic outbreaks in Russia could impinge upon the Company's profits due to business restrictions imposed to the Company and its contractors. In particular, there are risks of plant shutdowns, loss of productivity when switching to work from home, delays in the execution and implementation of commercial contracts, freezing of construction projects and repair jobs.
Launching a meat business project in the Primorye Territory involves a whole cluster of potential risk factors. The remoteness of the region where the construction is taking place from industrial centres, the lack of qualified white and blue collar staff and the difficult climatic conditions could potentially make the project more expensive and slow down its progress.
Climate change risks
Rusagro identified two main climate-related risks in 2021: lower revenues due to a drop in yields caused by abnormal weather conditions, and lower revenues due to the spread of animal and plant diseases.
Weather conditions are a critical success factor for the agribusiness. Extreme weather conditions and phenomena, such as droughts, frosts, excessive humidity, strong winds, hail and thawing, can erode crop yields, which determine the revenue size for all Rusagro's business segments.
Global climate change also brings the risk of dangerous animal and plant diseases, which can adversely affect the Company's performance. The most dangerous among them are root rots, parasites, viral and infectious diseases of pigs, such as African swine fever, reproductive and respiratory syndrome, foot-and-mouth disease and atypical pneumonia.
Sustainability risks
Risk description | Risk management | |
---|---|---|
Changes in laws, national policy and regulations | The Company monitors any changes in the national policy and responds accordingly, adapting Rusagro's strategy promptly The Company takes a proactive position and negotiates with government officials, whenever possible, the introduction of restrictive measures and their impact on business | |
Process-related errors | Monitoring and better management of the personnel, including through the elaboration of effective motivation systems Preparation and enforcement of standards, regulations and instructions for the process-related operations; Automation and digitalisation of planning processes, management of production activities | |
Reduced yields due to climate change and weather anomalies | An integrated approach to weather forecasting based on weather station data Regular monitoring of seeds Digitalisation of strategic planning and operational processes in the Agriculture Business Automated generation of the optimum schedule for sugar beet digging, piling and delivery, as well as the schedule for harvesting and delivery of grains and pulses Automated quality control of handling operations Development of sprinkling and irrigation systems Selection of the best hybrids and pedigree seeds to meet the condition of particular climatic zones | |
Escalation of costs associated with the meat business project in the Primorye Territory | The Company scheduled and is currently implementing the measures to protect its lands against natural phenomena common for the Primorye Territory, including the construction of additional surface water collection and drainage systems The construction contracted large-scale companies with their own logistics network both in Russia and abroad, in-house engineering and operation personnel. This increases the cost of project implementation, but mitigates the risk of longer timelines | |
Outbreak of an epidemic (among humans) in Russia | Establishment of a prompt response headquarters to develop anti-crisis measures and monitor their implementation Restricted movements of employees between the Company's offices and production sites, as well as less travel to other regions and countries Distribution of additional personal protective equipment and antiseptics, additional disinfection measures Comprehensive communication programme to keep employees informed, launch of dedicated hotlines for employees Support for employees to carry out regular testing and vaccinations | |
The spread of new animal and plant diseases | Transport and inventory flow control and decontamination Prevention of physical contact of farm-bred pigs with wild animals Health monitoring of pigs reared at the Company's production facilities Monitoring of ASF disease incidents in Russia Pest control by treating plants and seeds with insecticides and fungicides |
StakeholderS relations
gri 102-21gri 102-40gri 102-43gri 102-44Rusagro is in constant communication with its stakeholders including government authorities, own employees, local communities in the regions where the Company operates, consumers and investors. Rusagro uses appropriate channels of communication to make communication more effective.
The Board of Directors' consultation process with stakeholders is realized via the CEO of Rusagro, heads of the Company's business segments and heads of services responsible for interactions with the relevant category of stakeholders. The list of stakeholders is reviewed and updated on a regular basis.
Stakeholders engagement mechanisms
Stakeholders | Interest satisfaction measures | Communication channels / engagement mechanisms |
---|---|---|
Shareholders and investors | ||
Accommodating the interests of investors and shareholders regardless of geography, skill level, and the size of their block of shares is a high-priority task, which Rusagro completes through the timely disclosure of information about its activities and performance, in accordance with global best practice and the requirements of the Moscow Exchange and the London Stock Exchange |
| The Company's IR Director is responsible for liaising with representatives of the capital markets via the following channels of communication:
|
Employees | ||
The Company's employees are its most valuable asset and the foundation for sustainable development, therefore Rusagro invests significant resources in creating and strengthening internal human capital, building an attractive employer brand image and increasing employee engagement |
| The following channels of communication are used for internal communications:
|
Government and its agencies | ||
As a systemic company, Rusagro has a significant impact on the food security of the country and the well-being of the regions of its presence. The Company maintains ongoing cooperation with the state and its representatives to control political risks and support the accomplishment of national agenda |
| The Company is in a regular dialogue with the Government through professional unions (Russian Union of Sugar Producers, Russian Union of Pork Producers, Russian Oil and Fats Union) |
Clients | ||
Rusagro's clients are Russian and international industrial and trade enterprises operating in Russia and abroad. Further expansion of the customer base and stronger position in target markets is one of the Company's key priorities |
| The following channels of communication are used for clients engagement:
|
Community | ||
As a strategic investor, Rusagro is concerned about the social development and improvement of the quality of life in the regions of its presence |
| The Company uses the following channels of communication with local communities:
|
Membership of associations
gri 102-13As of the end of 2021, Rusagro is a member of the following industry organisations
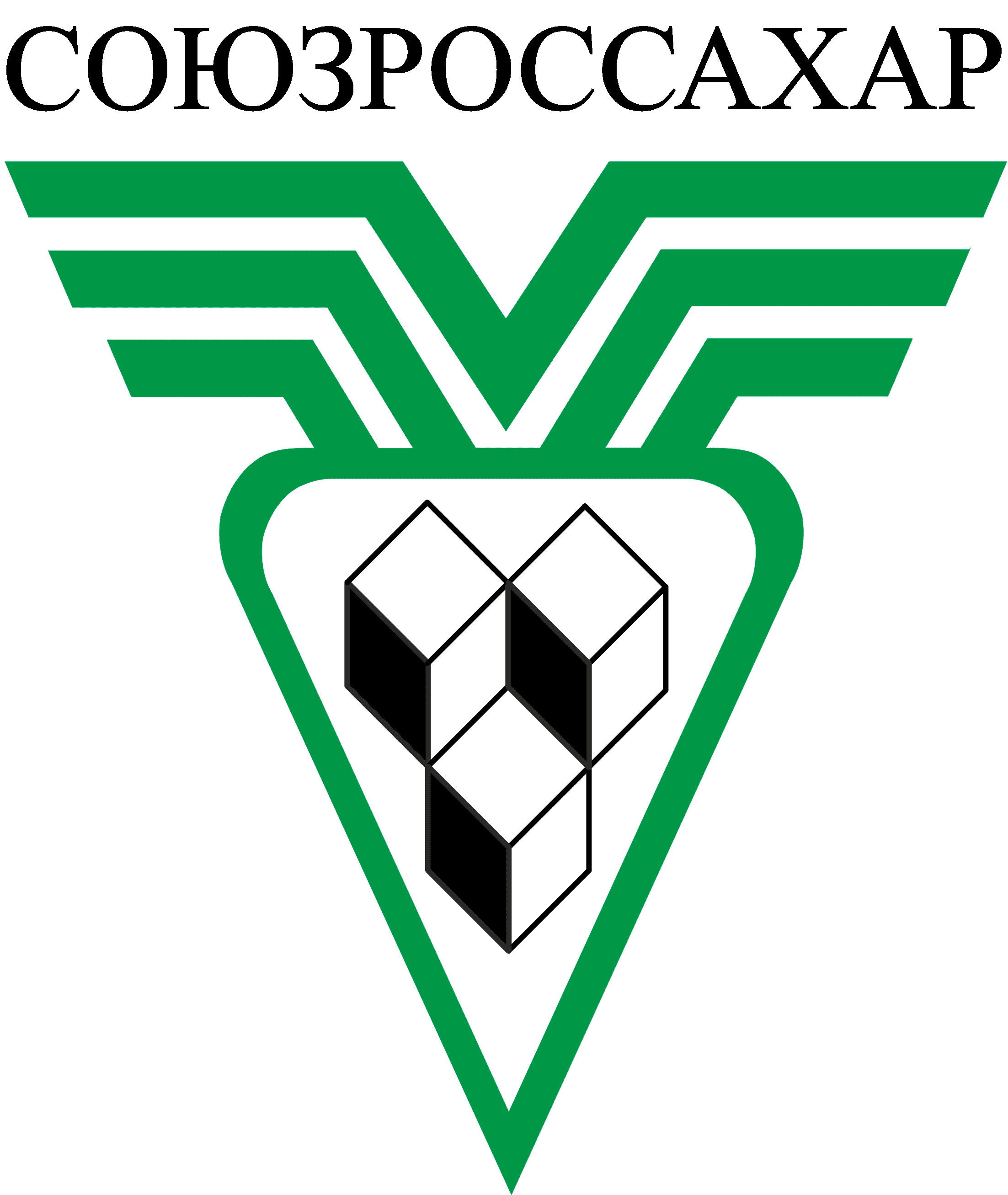
The Union of Sugar Producers of Russia is an organisation established in 1996 to coordinate the entrepreneurial activities of its members. The Union is also engaged in representing and protecting the common property interests of its members in state authorities and governmental bodies, Russian and international organisations. In addition, the organization applies its efforts to develop Russia's sugar beet industry and facilitate the effective functioning of the national sugar market.
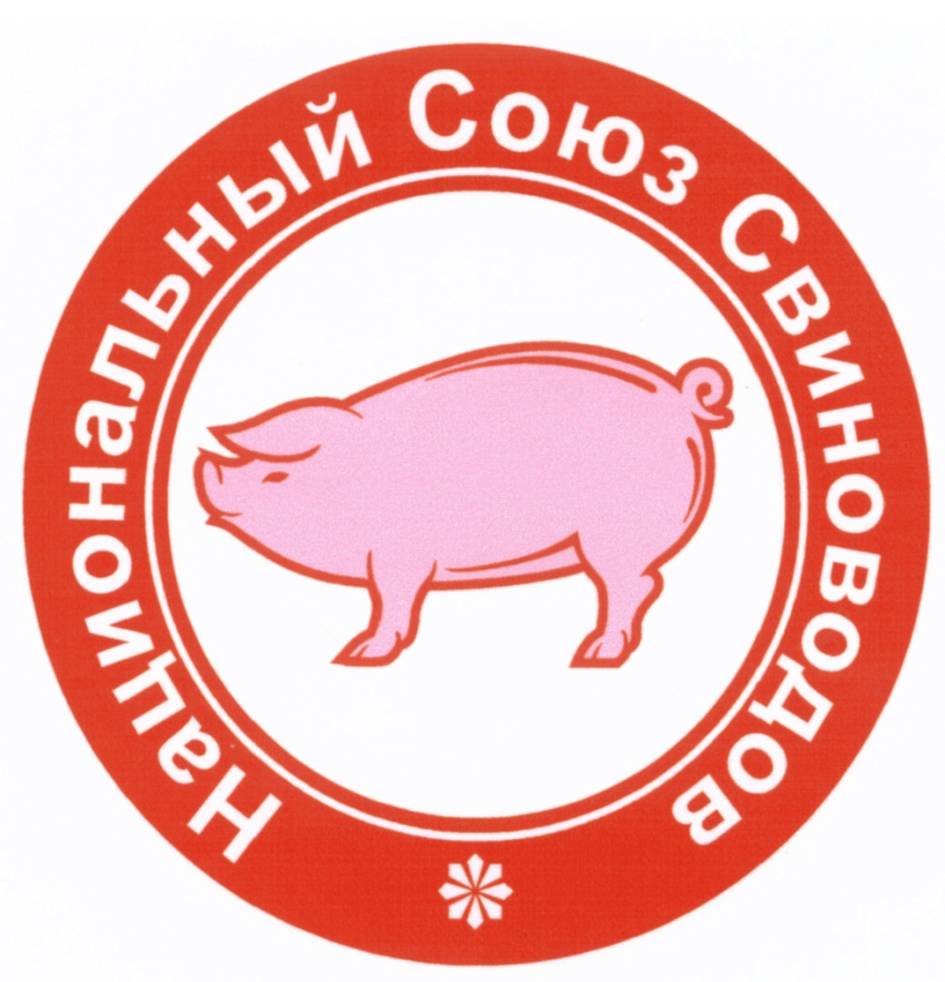
National Union of Swine Breeders is an association of Russian pork producers created in 2009 to coordinate their business activities, represent and protect their interests, and develop the Russian market for pork products.
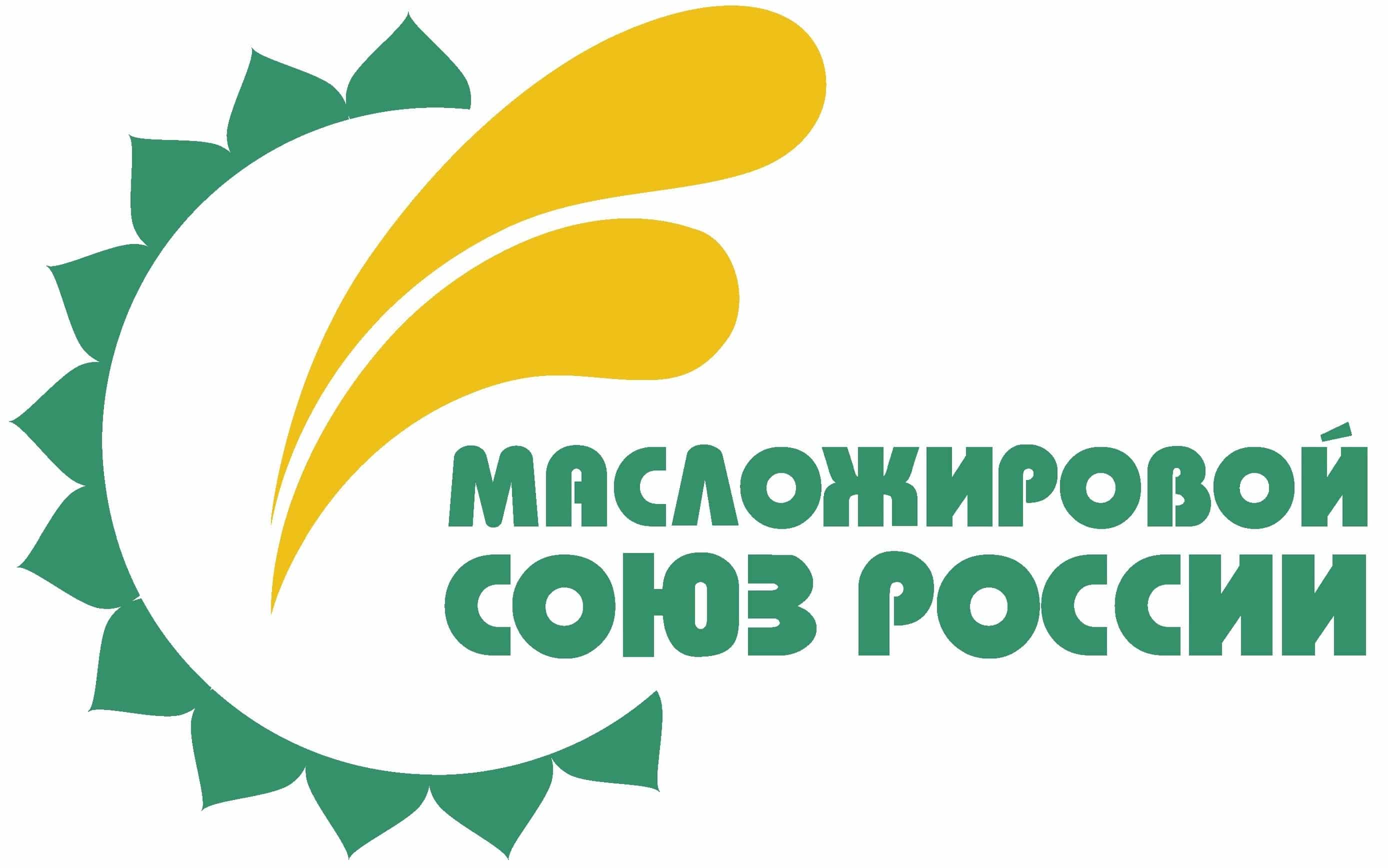
The Russian Oil and Fats Union is an organisation established in 1998 to consolidate the efforts and coordinate the activities of enterprises to ensure sustainable and stable functioning of the oil and fats industry in the country.
The Union cooperates with leading industry technologists, business representatives and is in close contact with the Chamber of Commerce and Industry of the Russian Federation, the Russian Union of Industrialists and Entrepreneurs, the Association of Manufacturers and Consumers of Oil and Fat Products, the National Association of Exporters of Agricultural Products and the Russian Export Center.
The organisation represents the interests of the oil and fats sector in the legislative and executive bodies of state power and administration, and participates in the development and implementation of state support measures for domestic producers.
Overview of the corporate governance system
Material TOPICS
- Diversity in the composition of governing bodies
- Performance efficiency of the Board of Directors
- Board of Directors and senior management remuneration
- Nomination of the Board members
GRI metrics
GRI 102-22 GRI 102-24 GRI 102-13 GRI 202-35 GRI 203-2 GRI 405-12021 highlights
CONTRIBUTION TO THE UN SDGs
Diversity of governance bodies
GRI 102-22 GRI 405-1
The collective experience and knowledge of the members of the Company's Board of Directors forms a favourable environment for constructive discussion of issues on the current agenda, ideas and proposals. Rusagro believes that the diversity of its corporate governance bodies in terms of gender, age, education, expertise and personal qualities is an undeniable advantage that allows the Company to be better at
The collective experience of the current Board of Directors covers a wide range of areas: agribusiness, economics and finance, corporate governance, audit, law and international policy, taxation and compliance. The share of women on the Board of Directors is 20%.
As of 2021, the average tenure of a Board member was nine years. The Chairman of the Board, Vadim Moshkovich, took office in 2015 and has not previously served on the Board of Directors. The term of tenure of other remaining members is 10 years as well. The average age of Board members is 46.
Matrix of competences of Board members
| | | | | |
---|---|---|---|---|---|
Agribusiness | + | + | |||
Economics and finance | + | + | |||
Corporate governance | + | + | + | + | + |
Audit | + | ||||
Law and politics | + | ||||
Taxation | + | ||||
Compliance | + |
Terms of tenure on the Board of Directors
years
| | | | | |
---|---|---|---|---|---|
Terms of tenure on the Board of Directors | 6 | 10 | 10 | 10 | 10 |
Age of Board members
years
| | | | | |
---|---|---|---|---|---|
Age | 54 | 73 | 59 | 44 | 46 |
PERFORMANCE OF THE BOARD OF DIRECTORS
Performance efficiency of the Board of Directors
The high efficiency of the Board of Directors was achieved through the high level of attendance and preparation for Board meetings. In the reporting year, none of the directors missed any Board meetings, demonstrating a 100% attendance rate. A total of four meetings of the Board of Directors were held in 2021. A list of the main issues considered by the Board of Directors during the meetings can be found in the Corporate Governance section.
The operating procedures for the Audit Committee are set out in the Regulations on the Audit Committee of the Board of Directors
Remuneration to the members of the Board of Directors
GRI 102-35The remuneration of senior executives is made up of a fixed pay and KPI-based bonuses. In addition to this, directors receive dividends as GDR holders.
In 2021, the total remuneration of members of the Board of Directors was RUB 1,188 mn, up 48% (or RUB 384 mn) above the 2020 base. In addition, members of the Board of Directors received RUB 1,479 mn worth of dividends in the reporting year, up 286% (or RUB 1,095 mn) year-on-year. Higher remuneration is a result of positive changes in its variable pay on the back of the Company's profit improvement in 2021.
Attendance at meetings of the Board of Directors and Board Committees in 2021
Vadim Moshkovich | Tassos Televantides | Richard Andrew Smyth | Anna Khomenko | Maksim Basov | |
---|---|---|---|---|---|
Board of Directors | 4 | 4 | 4 | 4 | 4 |
Audit Committee | N/A | 4 | 4 | 4 | N/A |
Nomination of new Board members
GRI 102-24Shareholders use the following key principles as guidance when setting up the Board of Directors
Members to the Board of Directors shall be selected as required by the applicable laws of the Republic of Cyprus and the Company's Articles of Association.
Ethical business conduct
Material TOPICS
- Business ethics and compliance
- Anti-corruption
GRI metrics
GRI 102-16 GRI 102-17 GRI 102-25 GRI 205-2 GRI 205-32021 highlights
CONTRIBUTION TO THE UN SDGs
Business ethics and compliance
GRI 102-16 GRI 102-25
Business conduct and ethics issues are addressed as governed by the Code of Business Conduct and Ethics of ROS AGRO PLC and Group companies approved in 2017. This document defines a list of mandatory rules to increase the capitalization, strengthen the reputation of the Company and maintain its financial stability and performance efficiency.
Management of compliance issues
Compliance management is structured through the Company’s Internal Audit Service (hereinafter – the "Service"). As stipulated by the provisions of the Code of Business Conduct and Ethics regarding compliance and adherence to the laws, the Service surveys employees for possible breaches of the law.
Compliance officers process complaints and make decisions on how to respond. Once appropriate checks are carried out, the results are discussed with the management with respective reports being prepared for the Audit Committee. It is also the responsibility of the Service to monitor the implementation of developed and approved compliance enforcement measures within the Company's operations.
If a violation of the law is identified, the
If a breach of the Code is not related to applicable law, the employee held accountable may be subject to sanctions such as disqualifying for bonuses or other incentives, withholding promotion or public sanctioning. The offender may also be subject to disciplinary action if
Avoiding conflicts of interest
Rusagro is cautious about situations in which an employee loses or may lose loyalty and objectivity towards the Company or the performance of his or her job duties. As potential conflicts of personal interest with the interests of Rusagro jeopardise the performance, the Company believes to have the right to prevent such situations, therefore the Company does not engage in any business relationship with customers, suppliers or competitors in any way other than in the course of conducting business on behalf of Rusagro.
The following situations are defined by Rusagro as conflicts of interest:
- romantic or amorous relationship between a manager and an employee accountable to that manager;
- kinship (close or distant) with another employee of the Company or a client, supplier or competitor;
- an employee of the Company (or a customer, supplier or competitor) is a spouse (including former spouses) or a relative;
- joint participation with another employee in a commercial enterprise, joint membership in religious or other non-profit organisations.
If such cases take place, the Code of Business Conduct and Ethics rules to have the immediate management and the Compliance Officer informed through appropriate channels of communication. A more detailed list of rules to avoid conflicts of interest can be found in the Code of Business Conduct and Ethics.
Anti-corruption
GRI 102-25 GRI 205-2 GRI 205-3 The Anti-Corruption Policy approved in 2019 is a main document that regulates the
No confirmed incidents of corruption were identified in the Company in 2021.
Key anti-corruption principles
The following key principles underlie the anti-corruption framework adopted in the Company:
- Non-acceptance of corruption in any forms and manifestations
- Personal example of the Company's management
- Employee engagement
- Consistency, balance between corruption risk and effectiveness of anti-corruption mechanisms
- Responsibility and inevitability of punishment
- Openness of the business
- Due diligence
- Continuous control and regulatory monitoring
- Compliance of the Company's Anti-Corruption Policy with applicable laws and generally accepted rules
Mechanisms for advice and concerns
GRI 102-17Compliance officers of the Internal Audit provide advice to employees on business ethics and compliance matters via email or telephone. The Internal Audit Service also receives, registers, records and analyses reports of instances of employees being induced to commit corruption offences for or on behalf of another organisation, corruption offences committed by Company employees, counterparties or other persons. In accordance with the Code of Business Conduct and Ethics, each whistleblower is guaranteed that his/her identity is protected, so he/she is free of any harassment.
The Agriculture Business launched an independent hotline in 2021, which is administered by a third-party operator. All calls are anonymous. The hotline gives direct access to the Ethics Committee, which consists of a narrow circle of top managers from the business segments. In addition to the telephone channel, concerns and statements can be sent via a special section on the website and email, which are also processed by an
Supply chain
Material TOPICS
- Responsible supply chain
- Circular economy and waste management
GRI, SASB metrics
GRI 102-9 GRI 102-10CONTRIBUTION TO THE UN SDGs
Management approach
GRI 102-9 GRI 102-10
Rusagro is committed to responsible supplier collaboration and supply chain transformation. Rusagro recognises the importance of creating a responsible supply chain and therefore has been raising sustainability standards by engaging with suppliers, regularly updating Rusagro's Tender Regulations across all business segments, and by optimising procurement activities.
The supply chain management approach is based on a continuous improvement model
Rusagro's supply chain management improvement process is aligned with the provisions of international documents such as the UN Global Compact, the Universal Declaration of Human Rights, the UN Guiding Principles on Business and Human Rights, and the International Labour Organisation Conventions.
The Company regularly updates corporate documents to improve the efficiency of procurement process and its transparency, as well as to achieve economic benefits for the Company: Rusagro's Tender Regulations, the Code of Business Conduct and Ethics, the Anti-Corruption Policy, and the Procurement Strategy.
Significant changes in the supply chain
In 2021, the Company effected significant changes in its approach to procurement and supply chain management.
Changes in the supply chain management approach
- separation of procurements into strategic and operational categories
- assignment of category managers responsible for the development and implementation of long-term strategies for assigned categories
- synergy in procurement of business segments
- promotion of central procurement framework within the Company
- expansion of best practices and staff competence development, more transparency of data and the quality of analytics
- improvement of procurement functions, centralised management of procurement categories in the corporate centre and creation of single transactional and contractual centre
Rusagro integrates sustainability goals and objectives into its supply chain management strategy.
Integrating sustainability goals and objectives into supply chain management strategy
Goals | Description of goals |
---|---|
Creating the equal competitive conditions for all participants |
|
Reducing the risk of transactions with compromised suppliers |
|
Putting stronger emphasis on supply chain sustainability |
|
Digitalisation and automation
Rusagro boosts process-related solutions aimed to optimise supply chain management procedures, e.i., a centralised SRM system for joint procurement, which was formulated in 2021 and currently is on the implementation stage. The projected return on this project is USD 0.5 mn. Rusagro's business segments are also rolling out programmes to implement industry-specific IT solutions for end-to-end process optimisation (projected return is about USD 1 mn).
Rusagro successfully launched the Digital Farmer application to automate the raw materials supplier management process. More than 1,500 agricultural producers in the three regions where the Oil and Fats Business operates are already using the app. In good time, we expect to roll out the app to other Rusagro regions as well. The Company also expressed a willingness to provide access to the app to non-competitors of Rusagro.
The objective of the platform is to simplify and improve the quality of Rusagro's interaction with farmers, make the processes more transparent, convenient and faster for all participants in the supply chain.
Supplier selection and interaction
The process of supplier selection starts with the evaluation of available proposals against compliance with the terms of reference and the quality of materials and services provided by the supplier. The Company's potential suppliers must be pre-qualified in order to meet our key requirements, including corporate social and environmental responsibility. The supplier is selected via an electronic trading platform for the electronic tendering system, which is used to identify critical suppliers, broadly divided into major suppliers, suppliers of critical goods and services, and non-substitutable suppliers.
The selection process is based on the criteria set forth by technical regulations, such as financial proposal, compliance with the terms of reference, business reputation, absence of tax debts, and compliance with the principles of due diligence. The supplier selection criteria may vary to meet the specifics and peculiarities of each business segment.
Description of the supply chain
Rusagro is working towards higher sustainability of its business and the entire supply chain. One of the Company's priorities is to develop and promote a circular and closed-loop supply chain. With the vertically integrated structure, business segments can minimise waste by re-using them. For example, the Agriculture Business uses defecate from the Sugar Segment as fertilizer.
- Business segments follow a category procurement strategy
- All procurements are divided into strategic and operational ones, thus allowing for optimisation of the procurement process
- With the Procurement Competence Centre launched in 2021, business segments are covered by a centralised procurement framework
- Business segments conduct a tender campaign based on the results of which a winning supplier is selected
- Those responsible for the business segments control supplies and supervise transactions as envisaged by the tender results
- Own transport and hired transport services are responsible for transportation
- The logistics companies are selected via the APLEX platform, which allows the Company to compare available proposals and choose the best ones
- The Company's business segments are members of the Charter of Carriers, which bolsters fair business conduct
- The business segments make sure storage facilities are running trouble-free and continuously
- Traffic safety departments give briefings and take preventive measures such as driver safety training, as well as supervise motivational and non-motivational programmes
- Energy accounting in warehouses is handled by the relevant technical services
Rusagro's strategy highlights four priorities in supply chain management, which are used to define key performance indicators in supply chain management.
Priorities in supply chain management and examples of KPI
- Costs saving
- Inventory and payables turnover
- Stock size
- Timeliness of procurement procedures
- Timeliness of provisions
- Requisition to contract/payment time
- Satisfaction surveys
- Staff competency assessment
- Share of employees with more than three years' experience in procurement management
- Number of training days per employee
Risks in the supply chain
SASB FB-AG-430A.3The Company has a unified Tender Regulations that define the basic requirements for the tender procedure, make sure that the principle of competitive procurement is respected and the procurement process is transparent as possible, while reducing procurement costs and thus mitigating the Company's risks along the entire supply chain.
The Regulation applies to all procurement areas for LLC Rusagro Group of Companies, as well as its business segments. For the reasons of objectivity, electronic bidding on an electronic trading platform is set as a common tendering method for all procurements. Tendering outside electronic trading platforms is allowed only if tender funds are below the established limits.
The Company has procedures in place to assess the good standing of suppliers and due diligence in the process of supplier selection. The development of a methodology for assessing supply chain sustainability risks is scheduled for 2022.
The supplier reliability assessment involves supplier background check through SPARK if run by the Service and through the Agribusiness Charter if run by the Procurement Department staff. If the results obtained show high risks, the supplier is blocked.
Plans for 2022 and a mid-term horizon
Rusagro plans to formalise the supply chain sustainability assessment process. At this stage, we have already started the supplier assessment in terms of quality, reputation and due diligence procedures. The Company also plans to develop an assessment methodology for supply chain sustainability risks.
Also, there are plans to implement a new supplier relationship management methodology, including supplier assessment and segmentation and supplier relationship development techniques to jointly optimise the supply chain), as well as intensify the interaction with Rusagro's strategic suppliers.
Product quality and customer safety
Material TOPICS
- Customer health and safety
GRI metrics
GRI 416-1 GRI 416-22021 highlights
for food safety management at meat processing plants under FSSC 22000 v5.1
of the BRAMS monitoring system for sanitory conditions of production sites and external territory at the pig farms in the Tambov and Belgorod Regions
of the raw material reception process in the Oil and Fats Business
the critical production parameter monitoring system at all sugar plants
CONTRIBUTION TO THE UN SDGs
Product quality management approach
GRI 416-1
One of the key priorities for Rusagro is client and customer satisfaction and safety. Each of the Company's business segments established its own product management and quality control framework to achieve high relevant performance results. All categories of finished products are assessed by quality control services to ensure that they do not have a negative impact on the health of customer.
Meat Business
The product quality management approach of the Meat Business is aligned with its Quality and Food Safety Policy. This System includes veterinary service, quality control and quality assurance service, standardisation and certification function, and claims collection and processing function.
The Company's veterinary service makes sure that animals are medically fit for use in food production, carries out an examination of finished products and draws up veterinary reports
The quality control service is responsible for quality control of all finished products. During 2021, Rusagro has been integrating a software that creates technology compliance checklists and assesses the quality indicators of the finished product.
The quality management approach at the production sites in the Tambov and Belgorod Regions was certified as compliant with ISO 22000 and FSSC 22000. In 2021, all sites in both regions have their documentation uniformed.
Claims management involved the collection of quality complaints from customers and their investigation together with the logistics and production departments.
Oil and Fats Business
The Quality Department of the Oil and Fats Business follows the provisions of the Quality and Product Safety Policy, Integrated Quality Management System Manual, Non-
All production sites are certified to ISO 9001 standard, and Yekaterinburg, Saratov and Atkarsk sites are also certified to FSSC 22000 standard. Following successful auditing in 2021, all sites confirmed their compliance with GMP+ standards. Saratov Fats Plant has RSPO ISCC certification.
The Quality Department of the Oil and Fats Business is also directly involved in auditing the Company's suppliers to ensure the quality of products purchased.
Sugar Business
The Quality Service is a department in the Sugar Business that is responsible for the coordination of all product quality assurance activities and the development of the quality management approach. This management body is present at all production sites. The Head of Security coordinates activities of the Quality Service at the business segment level, while the Site Quality Managers oversee quality control activities at separate production sites and supervise a plant chemical engineer (in charge of laboratory control) and a quality specialist (in charge of certification and incoming inspection).
All plants have a food safety management system compliant with
Agriculture Business
The product quality management issues in the Agriculture Business are covered by the Company's Commercial Function, reporting directly to the General Director of the Agriculture Business. The Function operates to Customs Union technical regulation 015/2011 "On Grain Safety", Rusagro's Quality Policy, instructions for quantitative and qualitative accounting of grain and its products, incoming quality control, drying and cleaning, storage of finished products, and regulations for crop production outgoing inventory.
There are four focus areas of the Commercial Function related to product quality management and control: laboratory control, assurance of system requirements for storage conditions, accompanying documentation and standardisation.
Priorities and key goals
Business sustainability necessitates continuous development of Rusagros' management system and product quality control.
Meat Business
- To fulfil stakeholder requirements:
- national traceability requirements
- changes to the National Certification System
- exclusive customer requirements
- entry into new high threshold markets
- Quality as a competitive advantage:
- compliance with market requirements
- ensuring the shelf life necessary for stable sales
- quality assurance in terms of shelf life and compliance with specifications;
- benchmarking of competing products
- High level of customer service (prompt feedback, objective and transparent feedback)
- WFP certification in export markets
- Cost-effective quality service
- Centralisation of the quality service
Oil and Fats Business
- To uplevel the quality of products made:
- to unify the quality control system at all stages: incoming control, production, control of finished products
- to upgrade the quality control of products made through internal inter-laboratory rechecks, inter-company rechecks with the involvement of third-party accredited laboratories
- to unify internal standards for finished products (B2B), semi-finished products
- To implement an operational efficiency plan:
- to reduce latent defects and returns from production due to non-conforming raw material;
- to ensure that the claims management process is efficient and effective
- to reduce the percentage of customer complaints
- To implement a site automation project:
- project for automated sampling at the stage when raw materials are transferred to the production, at the finished product outlet stage and at the shipping stage
- LIMS pilot project at one site with subsequent rolling-out
- to equip all sites with standardised high-tech equipment
- To upgrade the staff skills, ensure interchangeability of employees:
- to introduce common methodology training systems for employees
- to achieve human capital goals
Sugar Business
- Development and improvement of the food and feed safety and quality system
- Measurement efficiency improvement (through automation and implementation of statistical analysis methods)
- Focus on meeting customer specifications
- Focus on upgrading production culture and adopting lean production standards
Agriculture Business
- Conducting internal audits of elevators in terms of product quality
- Analysing the need and conditions for connecting express analysers at storage locations into a unified FOSS network
- Considering the replacement of manual quality control methods with methods involving automated equipment
- Ensuring reproducibility of quality indicators at all stages of the production process and during supplier and customer interactions
- Ensuring data entry into the Federal Grain Inspection Service system
Customers engagement
Effective communications with customers is a crucial tool in improving the quality of the products supplied. For this reason, each of Rusagro's business segments gives much attention to complaints and requests from customers and consumers.
In the Meat Business, claims management falls under the jurisdiction of the Customer Service Department, which structurally belongs within the Logistics Department. The common tools employed by the Customer Service Department to collect and process claims include a hotline, general
Most of complaints received can be divided into five categories:
Rusagro’s Oil and Fats Business has the Operational Support Service, a part of the Operational Directorate to cover the customer relations. The claims management of the Service is compliant with ISO 10002 and includes the processing of return requests, customer complaints and other customer requests. Available feedback options are website,
The majority of complaints received in the reporting year concerned documentation errors and price discrepancies.
The interaction channels with the Sugar Business's customers include
The Sugar Business carries out an
The Commercial Function of the Agriculture Segment is also responsible for communications with customers and partners, usually via postal service. There is a plan to create a spot and future trading exchange to support the tendering process.
Risk management
In pursuance of greater customer and consumer satisfaction, Rusagro closely monitors emerging product quality risks and tailors appropriate measures to prevent or minimise them.
Meat Business
Risk | Management activities |
---|---|
Product spoilage before the end of the actual shelf life declared by the producer | Sanitisation of production sites, including daily washing and disinfection of equipment and infrastructure. Monthly sanitation day for the complete treatment of the plants. The Quality Service and responsible units carry out an acceptance inspection of the workshops after each sanitation |
Procedures to improve sanitary conditions in the workplace include the issuance of clean protective clothing and personal protective equipment, washing and sterilisation of work tools, showering and hygiene treatment for staff on a daily basis. The Quality Service performs regular hygiene checks every shift | |
Control of process-related parameters, including control of compliance with specifications, exposure time and temperature of finished products, as well as room temperature and humidity conditions |
Annual risk reassessment is conducted by the Food Safety Group (HACCP); it can be carried out off-schedule in case of any changes in the technology or laws of the Russian Federation and the
Sugar Business
Risk | Management activities |
---|---|
Higher sugar outlet temperatures due to insufficient cooling capacity of the production line and inadequate storage conditions in the warehouses increase the likelihood of caking of finished products | Repair and upgrade of sugar refrigeration systems in plants and installation/upgrade of air conditioning systems in warehouses |
Foreign particles in the products due to corrosive wear of syrup collectors and product pipelines, deterioration of the silo lining | Timely repair/renovation of collectors and silos |
There is also a system of activities rolled out to the entire business segment, which is meant to improve control by the Quality Control Department, audit the food safety culture, and check that plants implement preventive and corrective product quality measures, as well as a revision of quality and food safety risk analyses.
Agriculture Business
Risk | Management activities |
---|---|
Poor quality of products received from the fields | Enhanced incoming product quality control – inspection of each vehicle |
Unsatisfactory condition of batches awaiting conditioning | Periodic control |
Deterioration of long stored batches | Periodic control at storage locations |
Poor quality of product shipped | Enhanced incoming inspection of goods shipped – inspection of each vehicle |
Oil and Fats Business
Risk | Management activities |
---|---|
Risks related to government and regulators | |
Changes in industry-specific legislation in consumer countries |
|
Lack of knowledge and non-compliance with laws and regulations due to incomplete external and internal documentation | |
Pecuniary sanctions or blockage of products produced | |
Supplier-related risks | |
Supply of products purchased that do not meet quality and safety standards |
|
Release of substandard products into free circulation without or with consumer health hazard | |
Infliction of harm to consumer health and potential damage to the company's image and reputation | |
Personnel-related risks | |
Assignment of ineffective and inefficient corrective actions |
|
Failure to implement preventive and corrective actions or to development and implementation of ineffective corrective actions | |
Re-occurrence of non-conformities, release of non-conforming products into free circulation | |
Risks associated with partners and outsourcing | |
Bioterrorism and sabotage |
|
Release of substandard products into free circulation without or with consumer health hazard | |
Risks related to the internal control system | |
Inadequate internal control system |
|
Release of substandard products into free circulation without consumer health hazard | |
Customer-related risks | |
Cross-contamination related to the acceptance of returned products that are overdue for sale |
|
Infliction of harm to consumer health and potential damage to the company's image and reputation |
According to the risk assessment methodology adopted in the Oil and Fats Business, existing risks
2021 highlights
GRI 416-2
Each of Rusagro's business segments defined an individual list of key performance indicators for quality management for 2021.
Meat Business
Key performance indicators established for the Company's Meat Business in 2021 cover the re-certification of the food safety management system and the minimisation of identified non-compliances of finished products and negative feedback from customers.
At the end of 2021, the Meat Processing Plant Quality Service in the Tambov and Belgorod Regions completed the digitalisation of the sanitary condition monitoring system for production areas and external territory of the BRAMS plant, involving the creation of a special software and the purchase of tablets to generate a checklist accommodating the priority requirements of production and the convenience of results analysis.
In 2021, 21 employees of Tambovsky Bacon underwent training at the Gorbatov Federal Research Centre for Food Systems. Fifteen of them successfully passed the final testing and received a selected taste-taster certificate – they are now entitled to professionally assess organoleptic characteristics of products.
The certificates obtained by the employees are valid for two years (until 2023), thus eliminating the need for additional external training in the near future. Internal training of the taste-taster certificate holders for the new product lines is scheduled for 2022.
Sugar Business
The KPIs of the Sugar Business Unit's Quality Service were primarily focused on reducing the number of customer complaints in relation to the quality of products supplied and certification of all production sites for compliance with FSSC 22000 and GMP+ standards.
The reporting year saw the implementation of a critical production parameter monitoring system running during the season at all of the Company's production sites to respond promptly to arising problems.
Agriculture Business
Similar to other business segments, the main efforts of the Agriculture Business's Quality Service were focused on the overall improvement of finished product quality and customer satisfaction. The Service's KPIs in 2021 were aimed to increase profits through higher product quality and reduce the number of negative feedback and counterparty complaints in relation to quality.
In 2021, the Agriculture Segment installed and made a trail run of an in-line analyser designed to control quality characteristics in the flow (protein). Some of the commodity flows were equipped with the necessary laboratory equipment, allowing the examination of quality
Oil and Fats Business
Quality KPIs defined for 2021 in Rusagro's Oil and Fats Business cover overall improvements in finished product quality and a reduction in the number of customer quality claims and
As Oil and Fats Business's production sites were to be re-registered as new legal entities, the Quality Service carried out extensive work to enter the new legal entities into the Mercury and Cerberus systems. The Service also obtained new approvals for finished products.
To facilitate the work with third-party suppliers, Rusagro established a mobile oilseed rapid quality assessment station in 2021. The Company audited the Evyap terminal in Turkey for sampling and determination of tropical oil quality indicators. The Quality Service of the Oil and Fats Business conducted nine supplier audits last year to assess the quality of products and services procured by the Company.
In 2021, there were no violations identified that resulted in fines, other penalties or warnings being imposed on the Company, as well as no violations of Rusagro's internal regulations and no violations recorded by state supervisory authorities.
In the first quarter of 2021, Rusagro automated its last oil extraction plant, which previously used to accept raw materials in manual mode. All laboratory analysis data can be now automatically entered into a database, eliminating the possibility of subjective intervention, and all agreed adjustments are applied automatically as well. The final results of the season are now
In 2021, seven sessions of interlaboratory controls were carried out between the laboratories of LLC Rusagro-Atkarsk,
In 2021, Rusagro made it halfway on a project to equip oil extraction plants with automatic samplers, on the Atkarsk site – for oilseeds, in on the Bezenchuk site – for oil, and at the Balakovo site – for meal.
These sites are pioneers needed to work out the details of the project and then roll out the results obtained to other sites in Rusagro's Oil and Fats Segment. The use of samplers will eliminate the human factor in sampling and increase sample reliability.
Plans for 2022
To meet customers' needs and provide them with high-quality food, Rusagro intends to further improve and develop its management and quality control system. In 2022, the Company will continue with the ongoing projects of its business segments. And moreover, there is a number of new activities and innovations we have in mind to improve the quality of our products.